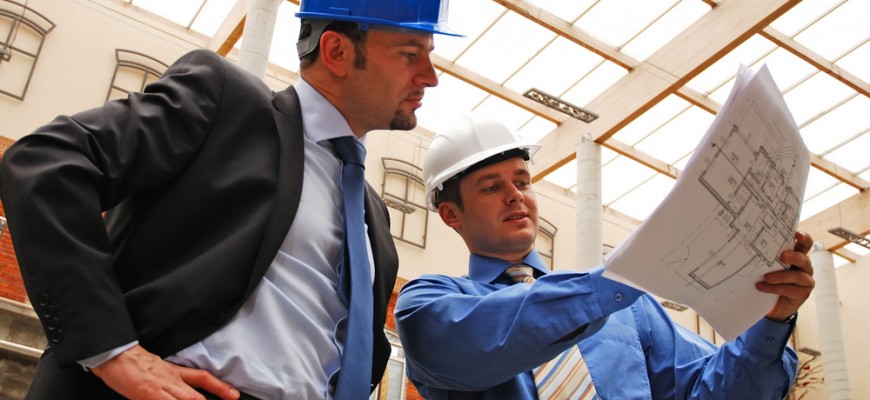
If you have a business that is responsible for testing the performance levels of elevator systems, you know that this can be a very comprehensive job. You are responsible for these devices which are taking people up and down what could be extremely tall buildings. Companies need to know that they are fully functional. There are many different components to an elevator, some of which are going to be extremely large. Others are going to be smaller components that will also contribute to the overall efficiency of this device. This is an overview of what an elevator system performance testing company will do for buildings throughout your city.
Different Components Of An Elevator
There are quite a few different components to an elevator. For example, this will include the car floor which is where people are going to be standing. There are what are called side portals, which are essentially the walls of the elevator itself. There is the car door track which is what allows it to line up with the floor that it is stopping on. Without it, you would not be able to simply walk out of the elevator as it would be a couple inches, or perhaps even a couple of feet, from being level.
There will be a unique floor covering which is typically made of some type of rubber, although carpeting can be used. There is the apron below which you will never see, and the kick plate which is accessible from inside of the elevator. There are car panels which represent the interior of the elevator, and there should be handrails for those that would need to hold onto them for safety purposes. Finally, there is the upper portal, blower fan, and the car ceiling which completes most of the components that make up elevators that are used today.
What Are Some Common Problems With Elevators That May Occur?
Some of the most common problems include elevators that do not have doors that open up properly. They may stop halfway, or they may not open for several seconds. This could be with the electrical timing, or some other problem that the elevator may have. It is likely an electrical circuit that needs to be repaired, yet it could also be something as simple as the elevator doors do not have enough lubrication to move out the proper time. Other problems may include the brakes. This can be very problematic.
If they are not able to stop, or if they completely fail, this could lead to a very problematic situation. This is especially important when you are installing these, or repairing these, in buildings that are over 10 stories. A free fall from that distance could cause significant problems for those that are inside of the elevator. There should also be access to the top through what is called the emergency trapdoor. This is often used to access the upper portion of the elevator where the cables and pulley systems are located. If that is not functioning properly, this could create a safety hazard for those that would need to be rescued if the elevator is stopped in between floors.
What If You Are Looking For One Of These Elevator System Performance Testing Companies?
If you are looking for one of these businesses, it may take you a few minutes, but you will always be able to find one. They are going to advertise like every other business out there. Most of the companies of the ability to send a representative out to first examine the situation. Once they have made a deduction as to what is wrong, and how they can fix it, you can then set an appointment.
You should do this for a couple different businesses. If you happen to be in a large city, there are probably a couple different companies that are offering these services. They should be able to come out, assess the problem within a few minutes, and provide you with an initial estimate as to how much it will cost. This might take a few days as not all of them will be able to send out a representative the same day that you call. Once you have the quotes back from these companies, you will know which one that you should use.
Reputation Versus Cost Of The Testing Services
The reputation of the company that you are working with is vitally important. This will ensure that you are working with a business that understands what they are doing. This will give you confidence that once they are done, repairs that they are making are going to be long-lasting and properly implemented. If you get a company that is charging less, make sure that you check on their reputation based upon online reviews or speaking with people that have also use their services. There is always a way to save money. They may even have a promotional offer that they are using when they are advertising to generate more clients throughout the month. Either way, your goal is to always use the best company, and secondarily find someone that offers the lowest prices possible.
Does It Take Long To Do These Inspections Or Repairs?
Elevator system performance testing is something that might take only a few minutes, or it could take several hours. It depends on what problems they are able to locate. For example, you could be working with a business that has been doing this for decades, and they will be well aware of the types of elevators that are out there, including yours. They will probably have some experience with restoring elevators that are currently experiencing your exact problem. At the very least, you should have one of these businesses come out on an annual basis to do inspections to make sure that they are functioning properly. You should never have to have them come back the next day as they will complete the repairs in a proper manner.
How To Schedule Your Appointment Today
It should not take very long at all to schedule this appointment. These businesses are often quite large, capable of dispatching someone out the same day that you call. If they are not, you might be willing to wait a day or two, especially if it is not an immediate problem. If it is an emergency, you will then need to contact a business that offers emergency services. Larger ones will have more employees that can be sent out to your location. If that is the case, you will then be able to have them restore your elevator if it is not functioning using the tools and expertise that they will bring.
Is This Likely To Be Repaired The Same Day They Come Out?
If problems are detected, they will try to fix the problem that they can the same day. If they’re not able to, they will tell you why. Sometimes it is a part or component that needs to be ordered that they do not currently have in stock. It might not be available anywhere in the city. If that is the case, they will give you a general idea as to how soon it will be sent to them. They can then schedule a time to come out to do the repairs. If you are in a building which has more than one elevator, this might not be a problem. However, if you only have one elevator, then you should try to find a company that has these components so they can do the repairs as soon as possible.
Locating elevator system performance testing companies doesn’t have to be difficult. If you are one of these companies, you should know how to advertise and find new clients. These are one of the more important businesses in large cities, especially those that have multiple skyscrapers that have elevators inside. Whether you are doing this for a large commercial building, casino, or any other building that has one or more elevators, just make sure that the company that you choose to work with is highly reputable and charges reasonable prices.